In a companion blog we investigated why and how precast concrete is prestressed. If you have not yet read that blog, we recommend that you do so before launching into this topic. We began by exploring the fundamental mechanics and performance of prestressed concrete beams in contrast with conventionally reinforced concrete beams, and then proceeded to describe typical production operations by which precast beams are prestressed. The purpose of this paper is to address the different means of achieving the desired prestressing force and the primary way of accomplishing the same goal of pre-compressing the concrete tensile zone by pre-tensioning the prestress strands.
Prestressed concrete is broken down into two (2) primary methodologies as described further below. The first method known as pre-tensioned, prestressed concrete is mostly used in the precast concrete industry. The second method known as post-tensioned, prestressed concrete is mostly used in cast-inplace concrete (also known worldwide as in-situ). Post-tensioned, prestressed concrete has subsets that will be described later.
The strands in pretensioned, prestressed concrete are tensioned prior to the concrete being cast. It requires substantial abutments or self-stressing steel forms capable of resisting these compressive forces to provide anchorage for the prestress strands. The process of pre-tensioning the steel strands involves placing the strands in the forms by “threading” them through the end abutments. Prior to placing the concrete in the forms tension is applied to the prestressed strands by using a hydraulic jack, after which they are anchored against the jacking heads by strand chucks. This concept is graphically depicted below.
After the fresh concrete has been placed in the forms, thus surrounding the pre-tensioned strands, the concrete is left to cure. The use of high-early strength cement in the concrete mix combined with accelerated curing methods usually results in the concrete products having sufficient strength to resist the applied prestress force and support their own weight when they are stripped from the forms after about twelve (12) hours. This accommodates a 24-hour production cycle of form setup, reinforcement placement, concrete casting, concrete curing, and product stripping for which precast, prestressed concrete is well-suited. The key take-away is the need for substantial abutments or self-stressing steel forms. The service lives of many of these abutments and forms frequently exceeds 50-years, making them natural solutions for precast concrete manufacturing plants.
The strands in post-tensioned, prestressed concrete are tensioned after the concrete is cast, thus it does not require substantial abutments or self-stressing steel forms used with pre-tensioned, prestressed concrete. Corrugated metal or plastic ducts are placed into the forms along with the reinforcement, after which the concrete is cast. After the concrete has reached sufficient strength, post-tension strands are threaded through the ducts, strand chucks are installed over the strands at each end of the beam, and the strands are tensioned using a hydraulic jack. The concrete strength is critical because the force of the strands is concentrated in this anchorage zone at each end of the beam, in contrast with pre-tensioned, prestressed concrete in which the force is evenly distributed along the length of the beam because the concrete completely engages the entire strand. The annular space between the inside walls of the ducts and the post-tensioned, prestressed strands is then pumped full of cementitious grout to engage the strands and provide protection against corrosion.
The image to the right shows a single strand chuck prior to placement at the end of the form at the termination of the duct. The plastic cone-shaped insert is temporarily used to form a recessed area into which the conical grip slips over the strand prior to jacking. After the strand is jacked the conical recess is patched with concrete to complete the process.
An advantage of post-tensioned, prestressed concrete construction is the ability to place the strands in a parabolic fashion to efficiently follow the bending moments resulting from the applied loads on the structure. Pre-tensioned, prestressed concrete construction is at a bit of a disadvantage regarding this feature and must revert to techniques, or a combination of techniques, using draped strands (sometimes called “depressed” or “harped” strands), additional parallel strands, or debonding strands. These techniques have their own design parameters and are outside the scope of this blog. The first image below shows how post-tensioned, prestressed strands are flexible and capable of being placed in a parabolic fashion across an elevated slab prior to the concrete being cast. The strands are designed and detailed to deliberately undulate up and down in response to the applied bending moment in the slab or beam. The second image below is a vintage photograph circa 1958 of a post-tensioned, prestressed, precast beam cast at Nitterhouse Concrete Products, Inc. This view of the beam clearly shows the nearly parabolic placement of the post-tension strands. It also demonstrates how post-tensioned, prestressed concrete is not limited to the world of cast-in-place concrete construction but can be used in a precast concrete production facility that lacks the abutment infrastructure previously described. Indeed, this beam was cast alongside Cleveland Avenue in Chambersburg, PA!
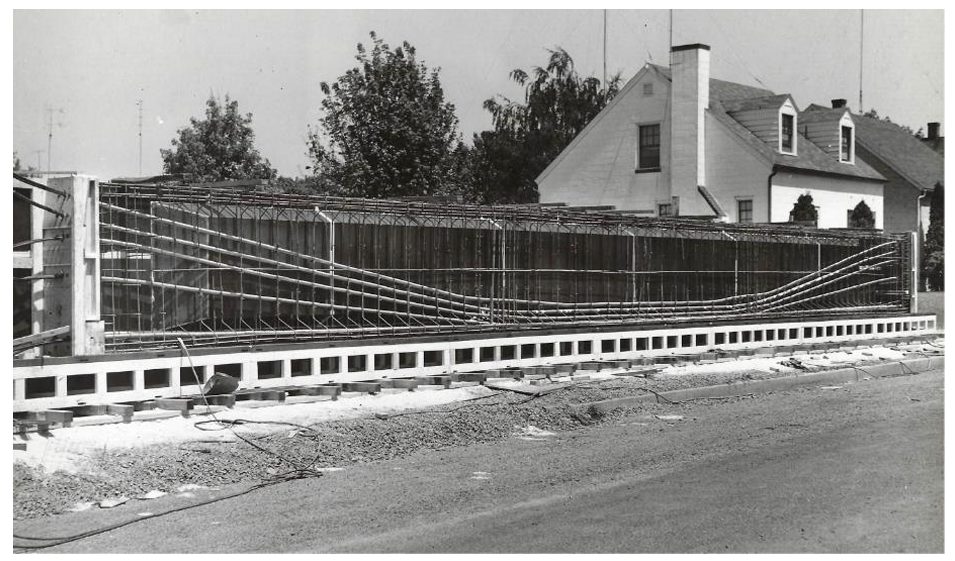
We made mention earlier in this blog that post-tensioned, prestressed concrete has subsets, one of which was already described by pumping grout into the annular space between the inside walls of the ducts and the post-tensioned, prestressed strands. This describes bonded post-tensioned prestressed concrete because as the superimposed loads are applied to the slab or beam, the strands impart uniform stresses to the surrounding concrete, emulating pre-tensioned, prestress strands which are naturally bonded directly to the surrounding concrete.
Another subset is unbonded post-tensioned, prestressed concrete as depicted in the image to the left. Instead of placing multiple strands within ducts, the individual strands are coated with grease and covered by a plastic sheath that is formed in an extrusion process. This provides permanent freedom of movement relative to the concrete. Unbonded strands provide better corrosion resistance, ease of construction, desired flexibility, and faster construction rate vs. bonded strands. Because the friction component of bonded strands is higher than unbonded strands additional bonded strands are needed to achieve the same load capacity as unbonded strands. Unbonded, post-tensioned, prestressed concrete does have the disadvantage of excessive crack widths and spacing under service loads when the concrete tensile stresses exceed the modulus of rupture. For this reason, since 1989 the ACI 318 code has included a provision for minimum bonded longitudinal reinforcement (i.e.: rebars) of 0.4% of Act for beams with unbonded tendons, and this provision continues in Section 9.6.2.3 of ACI 318-19.
On occasion precast concrete producers will utilize some unbonded, post-tensioned, prestress strands in their products to provide some compression to aid in shipping and erecting a variety of precast products such as architectural precast components, stairs, stadium risers, long columns, etc.
This is just a sampling of comparisons between pre-tensioned vs. post-tensioned, prestressed concrete that is intended to only touch on the basics. Indeed, chapters in textbooks have been written on this topic, which we would encourage one to pursue for a more thorough understanding.
Nitterhouse Concrete Products, Inc. (NCP) in Chambersburg, PA, has been family-owned and operated for five generations, serving the construction industry since 1923. Give us a call at 717-267-4505 or visit our website at www.nitterhouseconcrete.com for information on more quality precast, prestressed products to meet your design and construction needs. Choose with confidence and make NCP your single source for precast – what you need when you need it. Our experienced team of professionals is ready to help!